Personal Protective Equipment (PPE) Essentials at workplace
Safety cannot be compromised, particularly in hazardous environments like construction sites, healthcare facilities, and industrial settings. Hence, it is imperative that we prioritize safety to avoid any potential harm or casualties. Personal Protective Equipment (PPE) serves as the frontline defense, shielding workers from potential dangers. Correspondingly, it is crucial to have a comprehensive knowledge of Personal Protective Equipment (PPE), including its importance, correct application, regulatory requirements, and necessary training. Let us explore the essentials of PPE so that you can be well-informed about its significance.
Understanding PPE: What Exactly is Personal Protective Equipment?
Personal Protective Equipment, commonly known as PPE, encompasses various protective gear designed to safeguard individuals against workplace hazards. It acts as a barrier between the wearer and potential risks, including physical, chemical, biological, and radiological threats. Personal Protective Equipment (PPE) is designed to cater to the specific hazards present in the workplace.
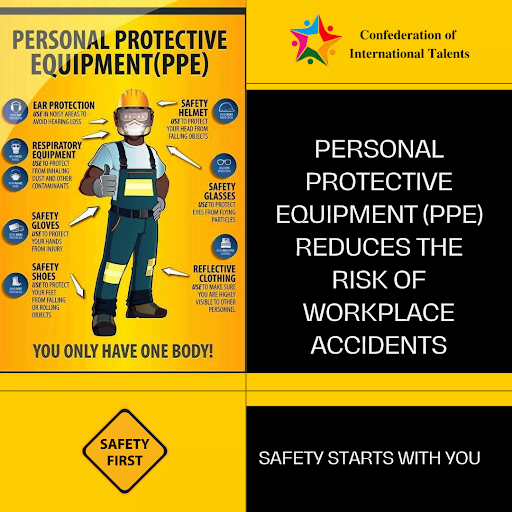
Why PPE Matters in Workplace Safety
PPE is not merely a precautionary measure; it’s a lifeline for workers operating in hazardous environments. Therefore, by providing employees with the necessary PPE, employers can build confidence among workers, promote a culture of safety, and ultimately enhance overall productivity.
How to Effectively Utilize Different Types of PPE
Each type of PPE serves a distinct purpose, and understanding their proper usage is imperative for ensuring maximum protection. Furthermore, by selecting, wearing, and maintaining PPE correctly, workers can mitigate risks effectively.
To ensure workplace safety, it’s crucial to understand how to effectively use different types of Personal Protective Equipment (PPE). Here’s a breakdown:
a. Helmets:
These protect your head from falling objects or impacts. Always wear them when there’s a risk of head injury. Ensure proper fit and check for any cracks or damage before use.
b. Safety Glasses:
Similarly, shield your eyes from debris or harmful substances. Wear them whenever working with tools or chemicals that may cause eye injury. Ensure they fit snugly and are clean.
c. Respirators:
Filter out harmful airborne particles, providing respiratory protection. Select the appropriate type based on the hazard and ensure a proper seal for effective filtration. Perform fit tests as per OSHA guidelines to ensure a secure fit.
d. Gloves:
Furthermore, protect your hands from cuts, chemicals, or other hazards. Choose the right type based on the specific task and ensure they fit well without hindering dexterity. Regularly inspect for any signs of wear and tear.
e. Protective Clothing:
Shields your body from various hazards like chemicals, heat, or biological agents. Wear appropriate clothing depending on the nature of the task. Ensure it covers your body adequately and is in good condition.
Regulatory Requirements: The Legal Framework Surrounding PPE
Regulatory bodies like the Occupational Safety and Health Administration (OSHA) have put in place rigorous guidelines regarding the usage of Personal Protective Equipment (PPE) in workplaces. Therefore, these guidelines are designed to ensure the safety of employees in hazardous environments. Consequently, as an employer, it is your responsibility to provide your employees with suitable PPE, conduct a thorough risk assessment of the workplace, and ensure that your employees are adequately trained in the use of the PPE provided. This includes proper fitting, maintenance, and replacement of PPE when necessary. As a consequence, failure to comply with these guidelines can result in hefty fines, lawsuits, and other legal repercussions. Thus, it is crucial to take the necessary steps to ensure that your workplace is PPE-compliant and that your employees are safe..
PPE Training: Equipping Workers with Essential Knowledge
Effective utilization of PPE necessitates comprehensive training programs. Therefore, employees should be educated on the importance of PPE, instructed in proper usage techniques, and familiarized with maintenance protocols. Regular Occupational Health and Safety Training sessions ensure that workers remain vigilant and competent in navigating potential hazards.
Frequently Asked Questions (H2): Addressing Common Queries About PPE
1. What are the Different Types of PPE?
- Helmets, safety glasses, respirators, gloves, safety boots, and protective clothing are among the various types of PPE available.
2. How Often Should PPE be Inspected and Replaced?
- PPE should undergo regular inspections for signs of wear and tear. Any damaged or outdated equipment should be promptly replaced to maintain optimal protection.
3. Are Employers Responsible for Providing PPE?
- Yes, under regulatory standards, employers are responsible for supplying appropriate PPE, conducting risk assessments, and ensuring proper training for employees.
4. Can PPE Substitution be Considered?
- PPE substitution should only be considered after a thorough risk assessment and consultation with safety experts. It should never compromise on the level of protection required.
5. What Should I Do if My PPE Doesn't Fit Properly?
- Ill-fitting PPE can compromise its effectiveness. Notify your employer immediately to arrange for proper fitting or replacement to ensure optimal protection.
Conclusion:
To conclude, Personal Protective Equipment (PPE) is not just a set of gear; it’s a shield of protection, a symbol of commitment to workplace safety. By understanding its significance, adhering to regulatory standards, and investing in comprehensive OHS training, we uphold the well-being of workers and maintain a culture of safety excellence. Utilize the power of PPE through an effective Occupational Health and Safety training program by CIT, Mauritius, and prioritize safety every step of the way.